Ultrasonic electrostatic transducers
Most common air-coupled transducers used in ultrasonic applications are either based on piezoelectric or electrostatic principles. Typically, piezoelectric transducers offer higher output pressure levels but have narrower bandwidth when compared to electrostatic transducers. In parametric sound applications, electrostatic transducers are usually used due to their inherent wide bandwidth and easy implementation of large aperture transducers. Electrostatic transducers are also well-suited for accurate distances measurements as very short duration signals can be generated and received, again, due to the wide bandwidth of the transducers.
Typically, an ultrasonic electrostatic transducer is composed of a flexible conductive membrane that rests on a conductive grooved back plate. When a DC biased electrical signal is applied between membrane and the back plate, the membrane moves towards or away from the back plate within the backplate grooves as shown in the figure below. If an ultrasonic signal is applied to the transducer the membrane vibrates and generates ultrasonic waves into the air.
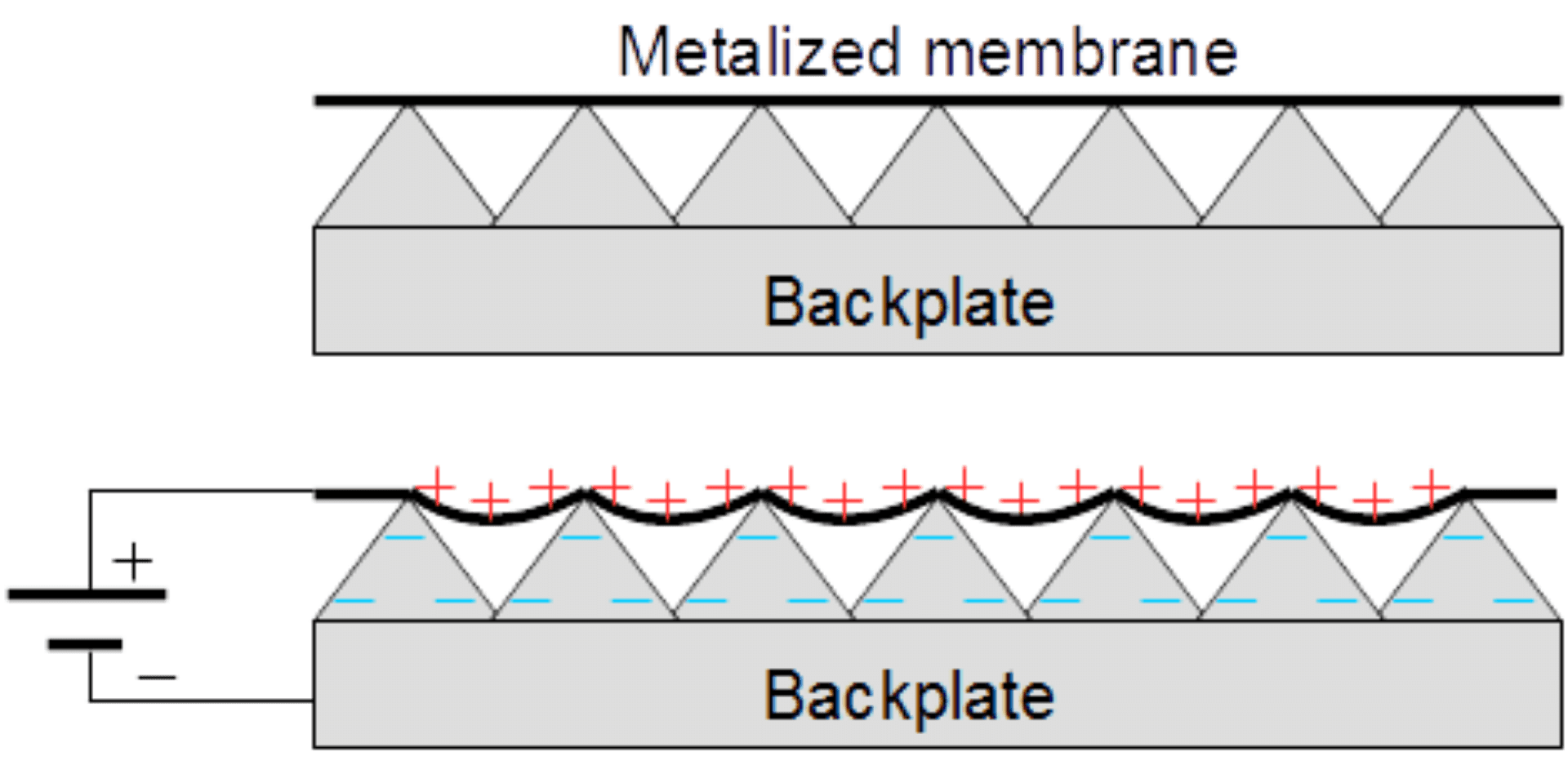
URG has developed electrostatic transducers and their manufacturing method based on a PCB manufacturing processes. The major novelty introduced by URG is that a PCB board with etched traces deposited with solder metal is used as a backplate for the transducer. The use of PCB manufacturing technology allows easy customization of transducers as the electrodes in the backplate can be arranged in virtually limitless configurations. Therefore, transducer can be tuned to have certain pressure field characteristics or, say, a phased-array system can be implemented on a single back-plate. Moreover, the driving electronics for the transducer could be implemented on the same PCB board that is used as transducer's backplate, which would allow shrinking the size of final products.
Patents
Putkis, O., Vanagas, G., Mikolajunas, M. and Virzonis, D., 2020, Method for generating parametric sound and means for carrying out said method, patent application WO2020026005.